Financial News
Specialism Included as Standard in Starrag Machines
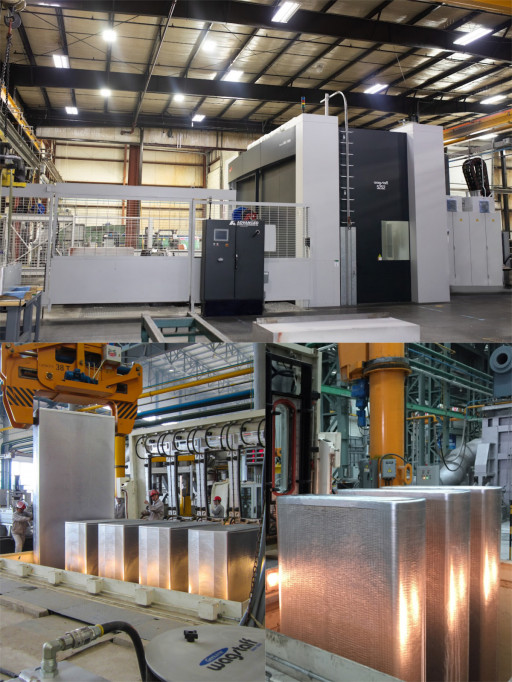
\"The Starrag machine can easily process\ncomplex workpieces with edges up to\n118 in. (3,000 mm) in length and weighing\nas much as 17,637 lb. (8,000 kg).\"
HEBRON ESTATES, Ky. - November 29, 2021 - (Newswire.com)
James Kuntz, Wagstaff's Hebron, Kentucky USA Plant Manager, wanted to locate a new CNC machining center to streamline the process of machining support blocks. The blocks are key components that guide their respective continuous casting bar during the casting process. "We looked at lots of machines…but we couldn't find one capable of handling the wide range of parts for our systems."
Kuntz contacted a colleague who directed him towards Starrag machines. "The Heckert HEC 1800 was the only machine to offer a sufficiently large working area for us to produce our parts. Despite all our research, we didn't find another machine that even comes close to offering what the Heckert HEC 1800 does."
"Many machinery suppliers offer expensive custom solutions — but with the Heckert HEC 1800 and simple optional adjustments, Starrag gave us a machine that enables us to create complex customer-specific solutions for a wide range of applications," says Michael Wagstaff, CEO of Northern Kentucky Operations at Wagstaff, Inc.
Wagstaff continuous casting systems can simultaneously produce 1 to 160 round-bar blanks with a diameter between 4.33 in. (110 mm) and 48.54 in. (1,223 mm) in each pass. The rectangular bars can be cast in many sizes and diameters, reaching over seven meters in length and weighing over 40 tonnes. The Starrag machine can easily process complex workpieces with edges up to 118 in. (3,000 mm) in length and weighing as much as 17,637 lb. (8,000 kg). In response to these machine engineering requirements, the Heckert HEC 1800 horizontal machining center has been designed in a flexible and modular way to ensure optimal results for many sizes, weights and alloys during machining.
Ambitious goals and promising results
Kuntz says that integrating the Heckert HEC 1800 into Wagstaff's production facility has significantly reduced the time it takes to produce customer-specific support blocks. "The machine saves time and can work without supervision. What's more, the workpieces are ready for assembly after machining without the need for further processing. We're particularly pleased with the machine's reliability, which makes it extremely efficient. The Heckert HEC 1800 has been operating at over 95% capacity for several months, so it's almost working continuously."
Michael Wagstaff, CEO of Wagstaff Northern Kentucky Operations, says, "We usually produce batches of four to six aluminum support blocks for our customers. These support blocks need clamping in sizes up to 30 in. by 90 in. by 15 in. (762 mm x 2,286 mm x 381 mm) — that's our typical workpiece. It used to take 10 hours to produce workpieces like these, but we wanted to reduce that to four and a half." Kuntz justifies the objective with recorded progress from Wagstaff's production environment, "We're now at five hours and have fewer and fewer manual tests to perform during the process. We're getting better and better, and are confident that we'll have reduced our production time by 55% as planned very soon."
In reference to metal type, hundreds of different alloys have already been processed on Wagstaff casting systems. Many new and existing alloys for general and aerospace applications are continuously being tested for future use in Wagstaff's industry-leading research and development lab.
Wanted: a big and powerful solution
"We place very particular demands on our machining centers, which explains why it took so long for us to find the right one. But the Heckert HEC 1800 already met so many of our machining needs…we only had to make one small optional adjustment to cover our entire portfolio of applications," says Kuntz. Wagstaff had originally planned to use five-axis machining, but the Heckert's working area made it possible for workpieces to be extensively machined with one less axis and without having to be re-clamped. As a result, Wagstaff improved machining quality and shortened production set-up times.
The Heckert HEC 1800 offers a wide range of work spindle options, process-optimized solutions for tool and workpiece handling, and innovative process control and monitoring systems. Wagstaff notes, "We chose a 15,000-rpm motor spindle and torque values that suited our applications. This spindle was the right choice for us to deliver the necessary torque when deep-hole drilling and contouring the aluminum blanks."
"Exactly," says Kuntz, "We have a customer who needs his support block to be manufactured from blanks made of 7000-series alloys. The Heckert HEC 1800 is completely unfazed by this high-strength aluminum, meaning we can meet our customer's requirements efficiently and effectively."
Ultimately, however, it wasn't just the machine's selling points that won over Wagstaff. "We were drawn to Starrag because of its global team of support staff who wholeheartedly stand by their products. The company is more than a supplier to us — we consider Starrag a partner. That's very important to us."
Company profile Starrag
High-precision machine tools for greater productivity
Starrag Group is a global technology leader in manufacturing high-precision machine tools for milling, turning, boring and grinding workpieces of metallic, composite and ceramic materials. Principle customers are internationally active companies in the Aerospace, Energy, Transportation and Industrial sectors (Industrial Components, Luxury Goods, Med Tech). In addition to its portfolio of machine tools, Starrag Group provides integrated technology and maintenance services that significantly enhance customer quality and productivity.
The umbrella brand Starrag unites the product ranges Berthiez, Bumotec, Dörries, Droop+Rein, Ecospeed, Heckert, Scharmann, SIP, Starrag, TTL and WMW. Headquartered in Rorschach/Switzerland, the Starrag Group operates manufacturing plants in Switzerland, Germany, France, the U.K. and India and has established a network of sales and services subsidiaries in the most important customer countries.
The shares of Starrag Group Holding AG are listed on the SIX Swiss Exchange.
For more information:
Starrag
Elena Schmidt-Schmiedebach
Lead Marketing North America
Mobile: +1 (859) 380-2356
www.starrag.com
Press Release Service by Newswire.com
Original Source: Specialism Included as Standard in Starrag Machines
Stock quotes supplied by Barchart
Quotes delayed at least 20 minutes.
By accessing this page, you agree to the following
Privacy Policy and Terms and Conditions.